In-situ capability assessment for rail repair via additive manufacturing
Funded by Innovate UK, 91Ö±²¥ have been developing laser cladding methods for repairing rail using like-on-like materials.
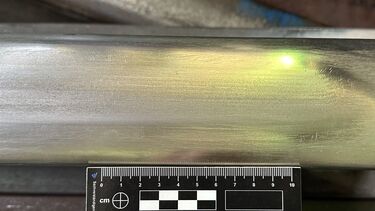
Laser cladding offers precise targeting of the damaged area of rail, requiring significantly less heat input compared to traditional methods like welding. The reduction in heat input reduces the chance of a Heat Affected Zone (HAZ) damage to surrounding rail material. The process has the potential to be applied in-situ, reducing the amount of line possession time required. Laser clad coatings for application on rails in full lengths for the purpose of life extension has undergone successful field trials for improving wear resistance of new track components using the application of premium materials.
In this project short lengths of R260 grade rail and HP335 rail were repaired with laser cladding. The process involved machining out material following the welding standards for rail repair, pre-heating the rail and applying the laser cladding, built up in layers until the section returned to just above profile, and a final machining stage was then complete to return the rail to the original profile. This was done within a workshop to ensure quality of repair, whilst using techniques which could be translated to in-situ application in following project phases. Repairs were complete at depths of 3 and 9 mm, the first time this method has been applied to depths of greater than 2 mm. R260 grade rail steel metal powder was used to repair the R260 and HP335 rails; to minimise waste and keep future application costs lower for maintenance teams.